Modules
Designed to equip your organization with the tools needed to enhance efficiency and eliminate losses. With a bottom-up approach that prioritizes the shop floor, Plant Toolbox centralizes loss elimination data into one place and offers a scalable solution that grows alongside your business.
As information is generated or updated in one module, it directly influences and enhances the functionality of the others, creating a cohesive and efficient system that drives continuous improvement across your entire operation.
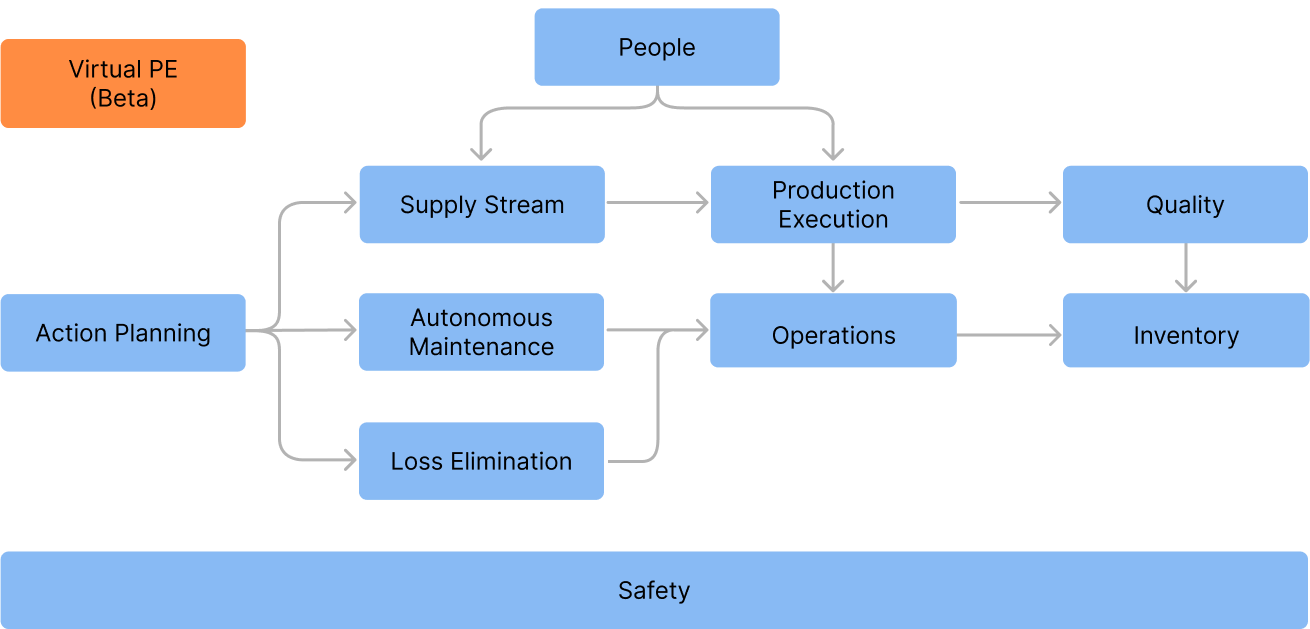
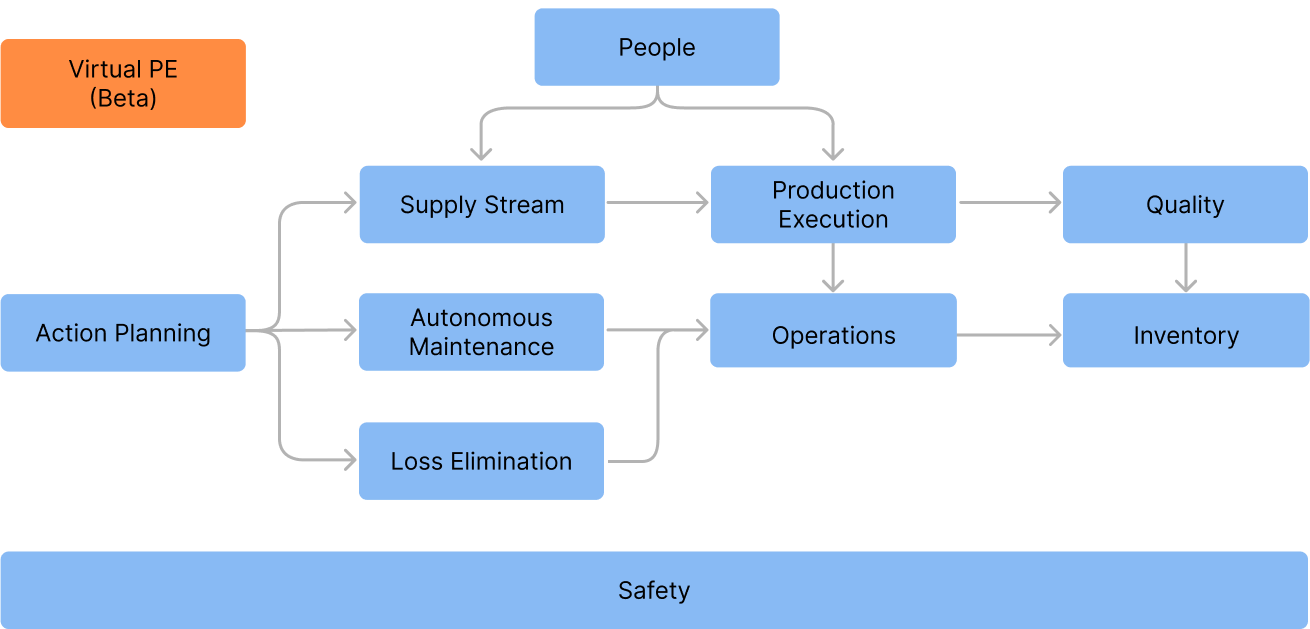
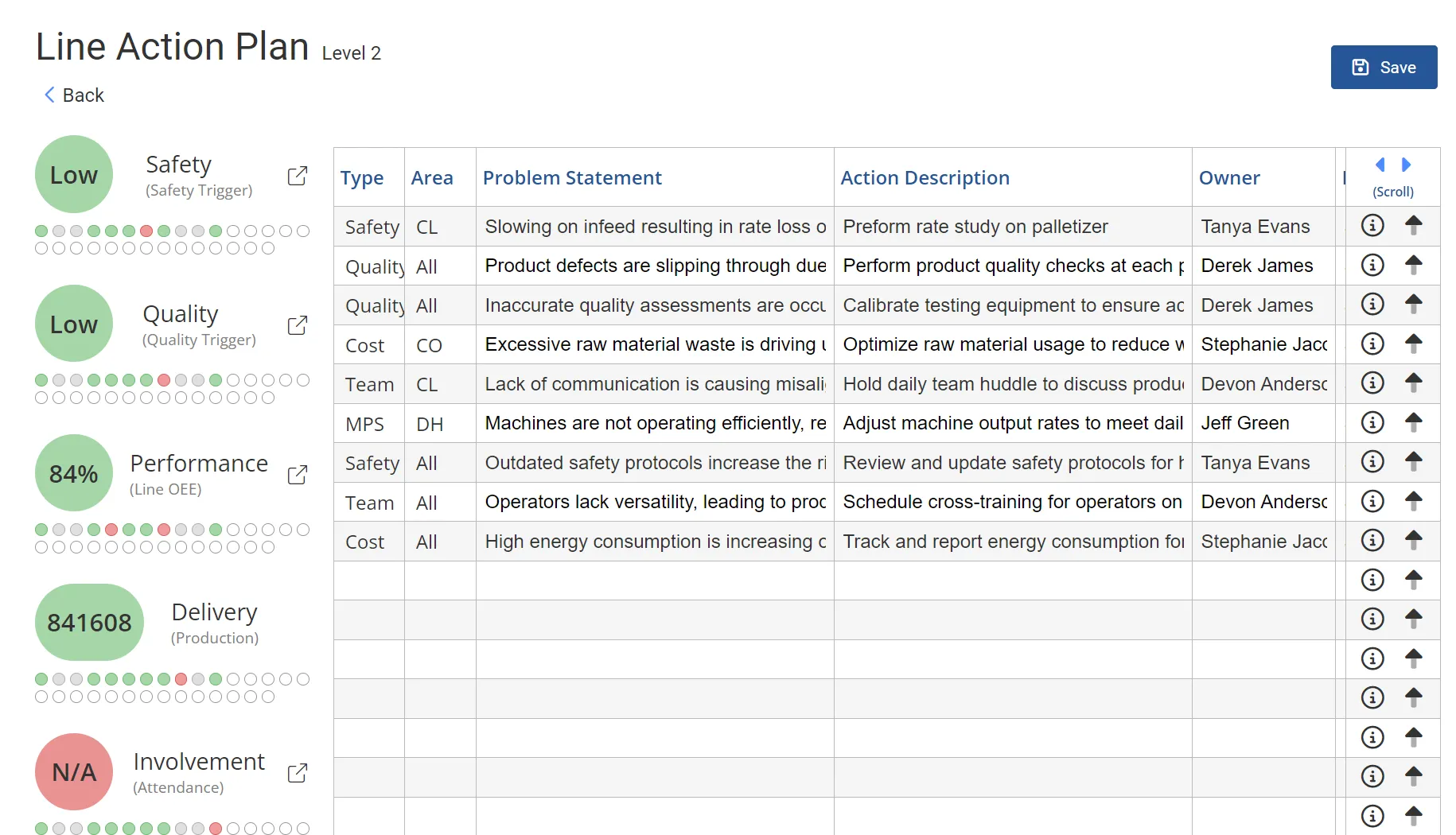
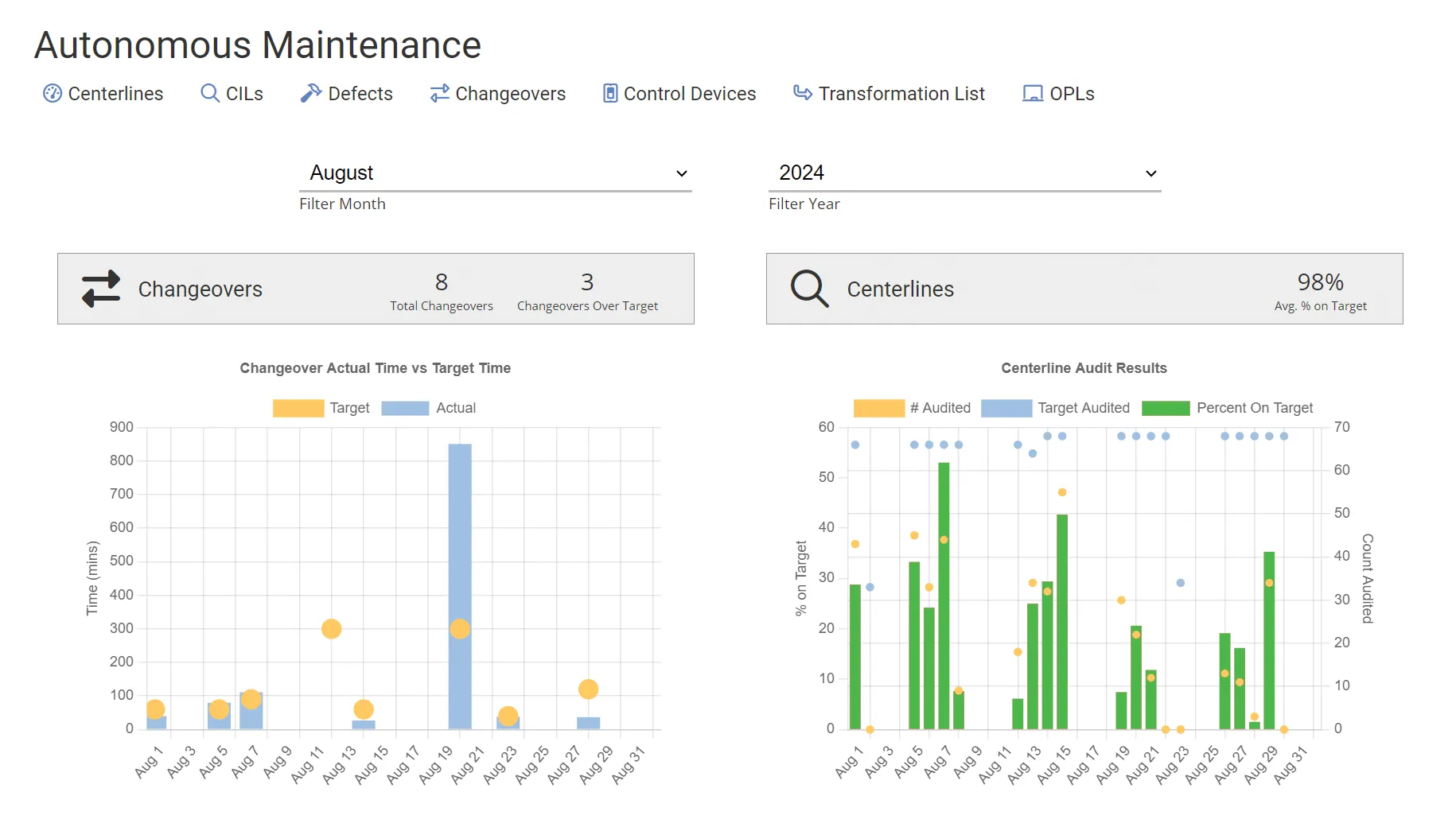
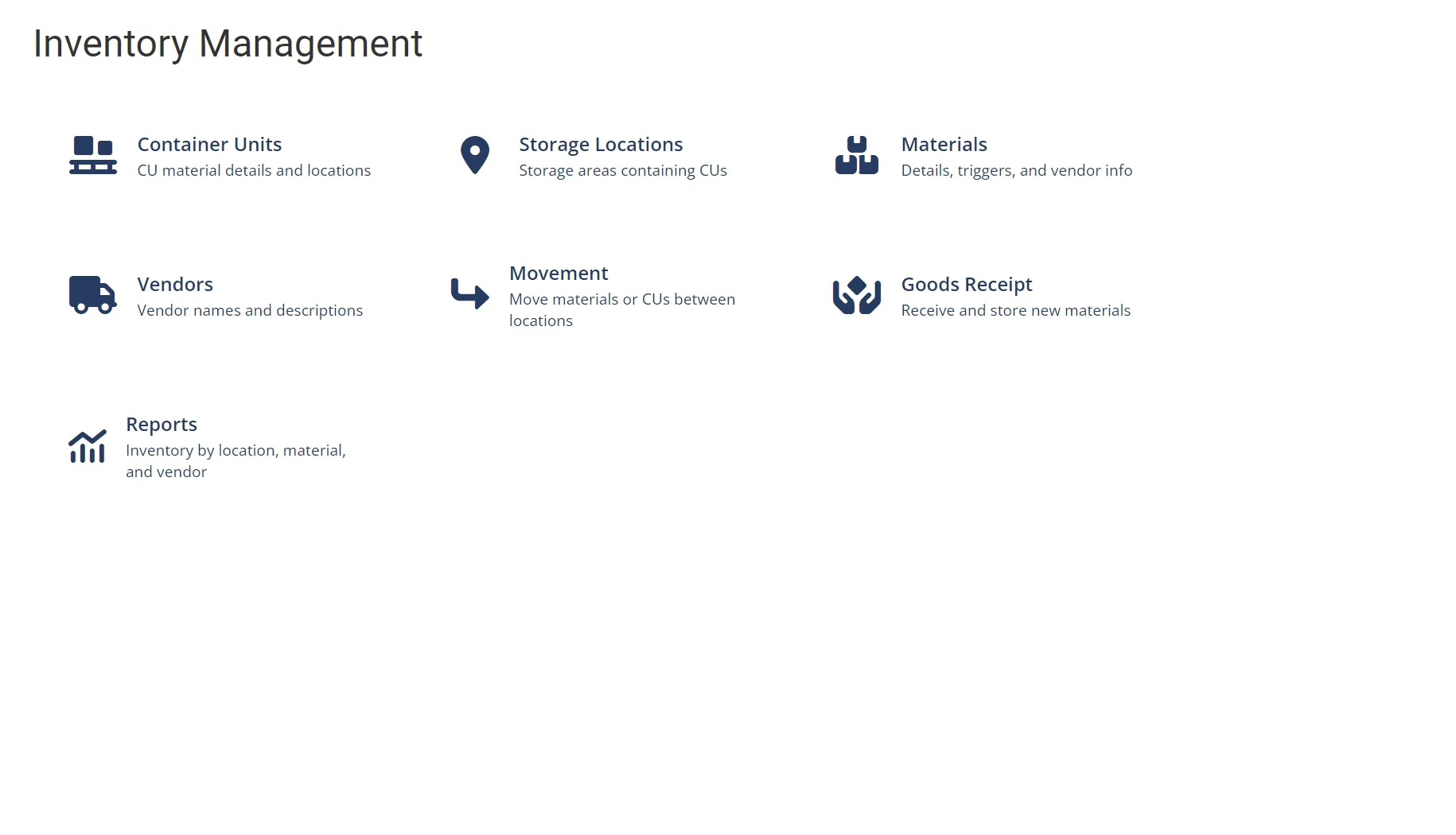
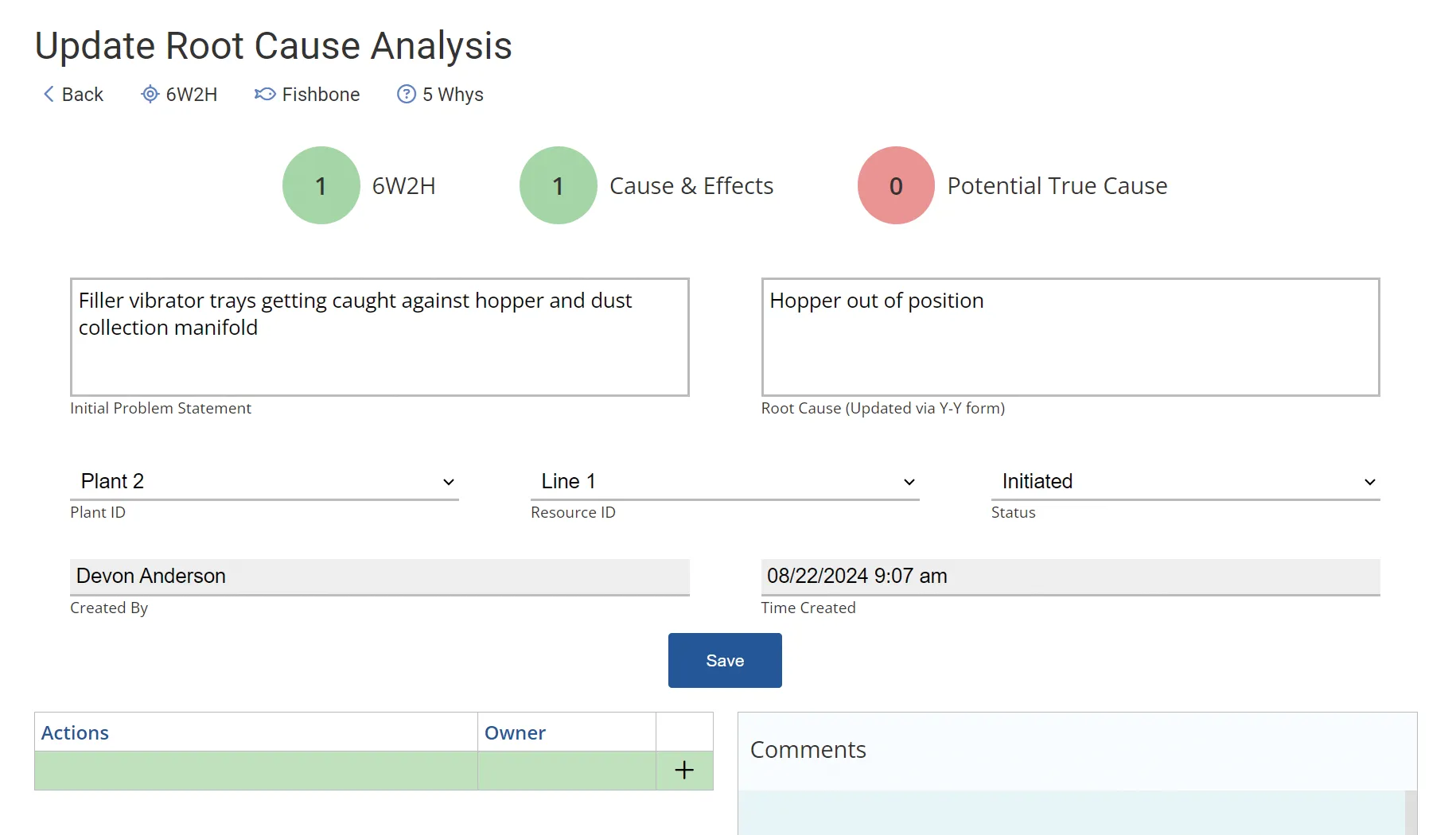
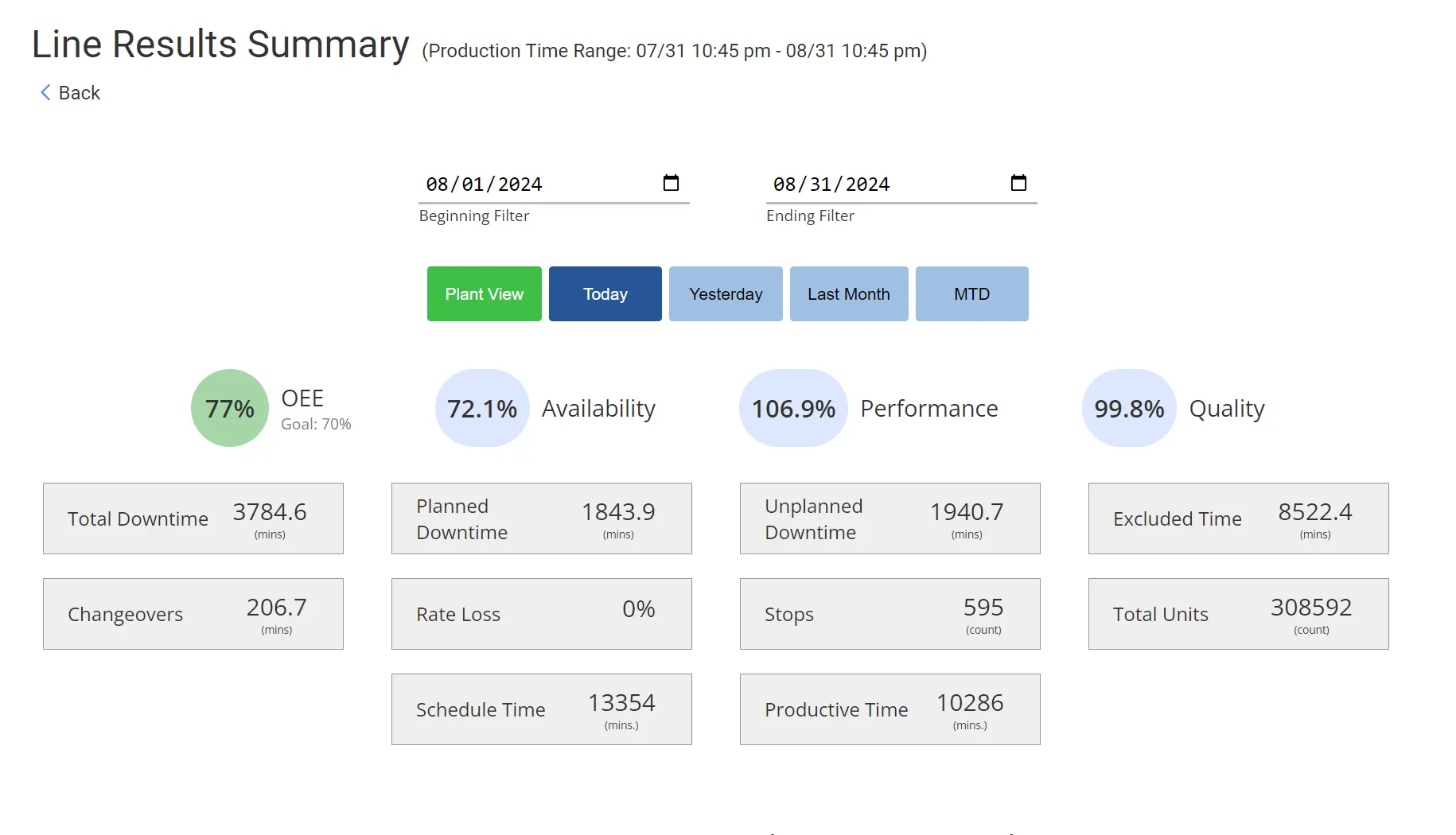
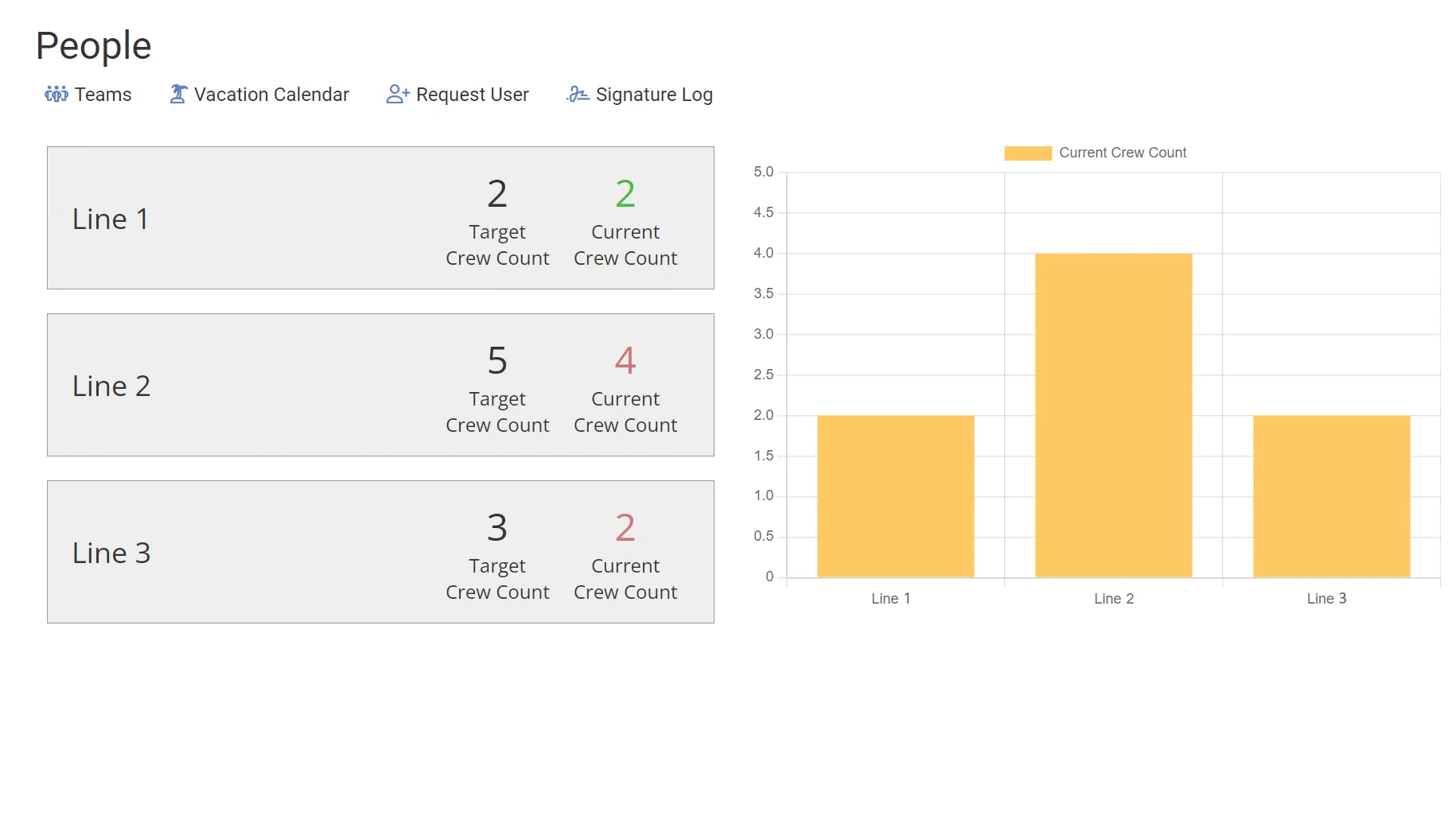
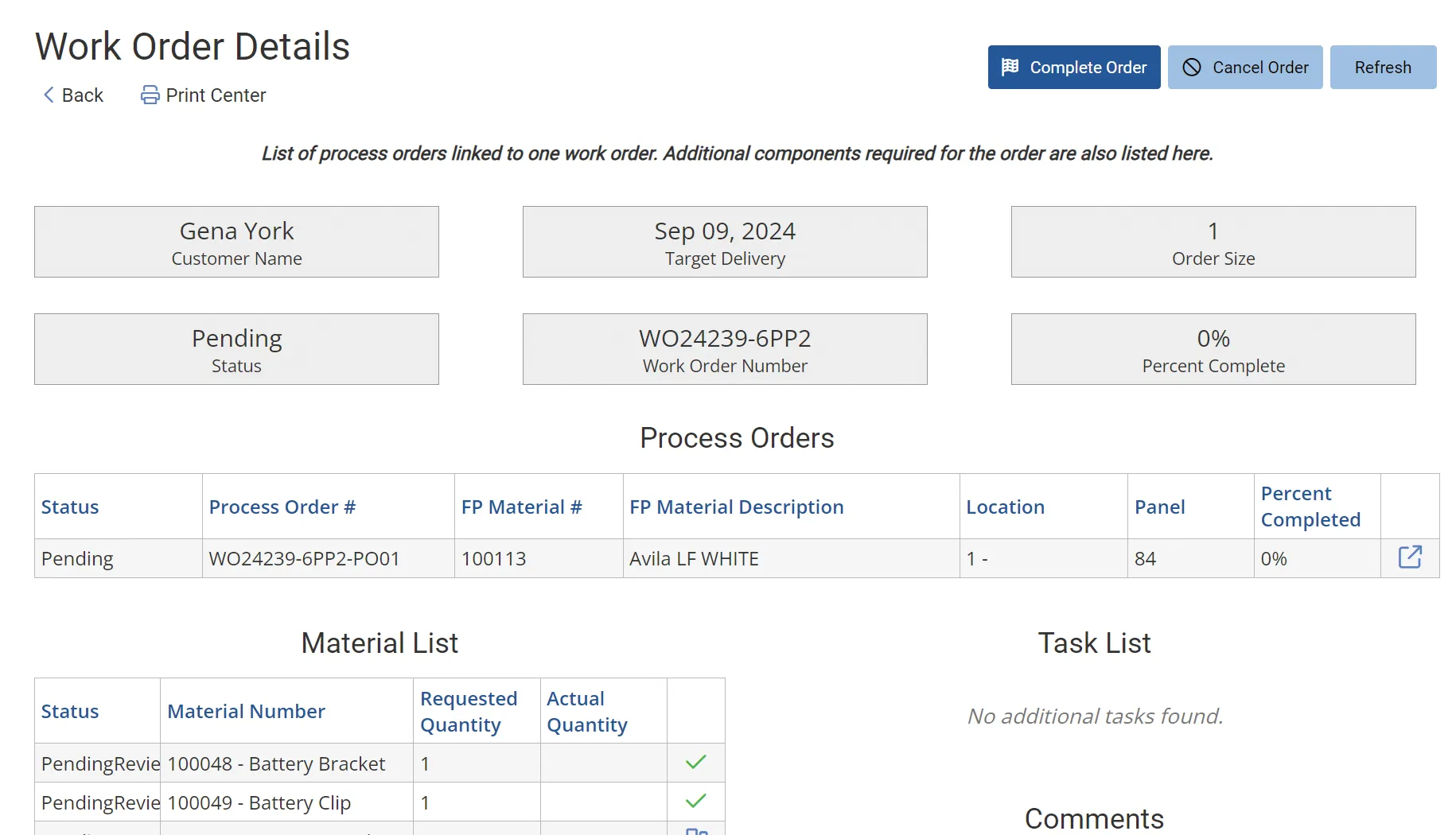
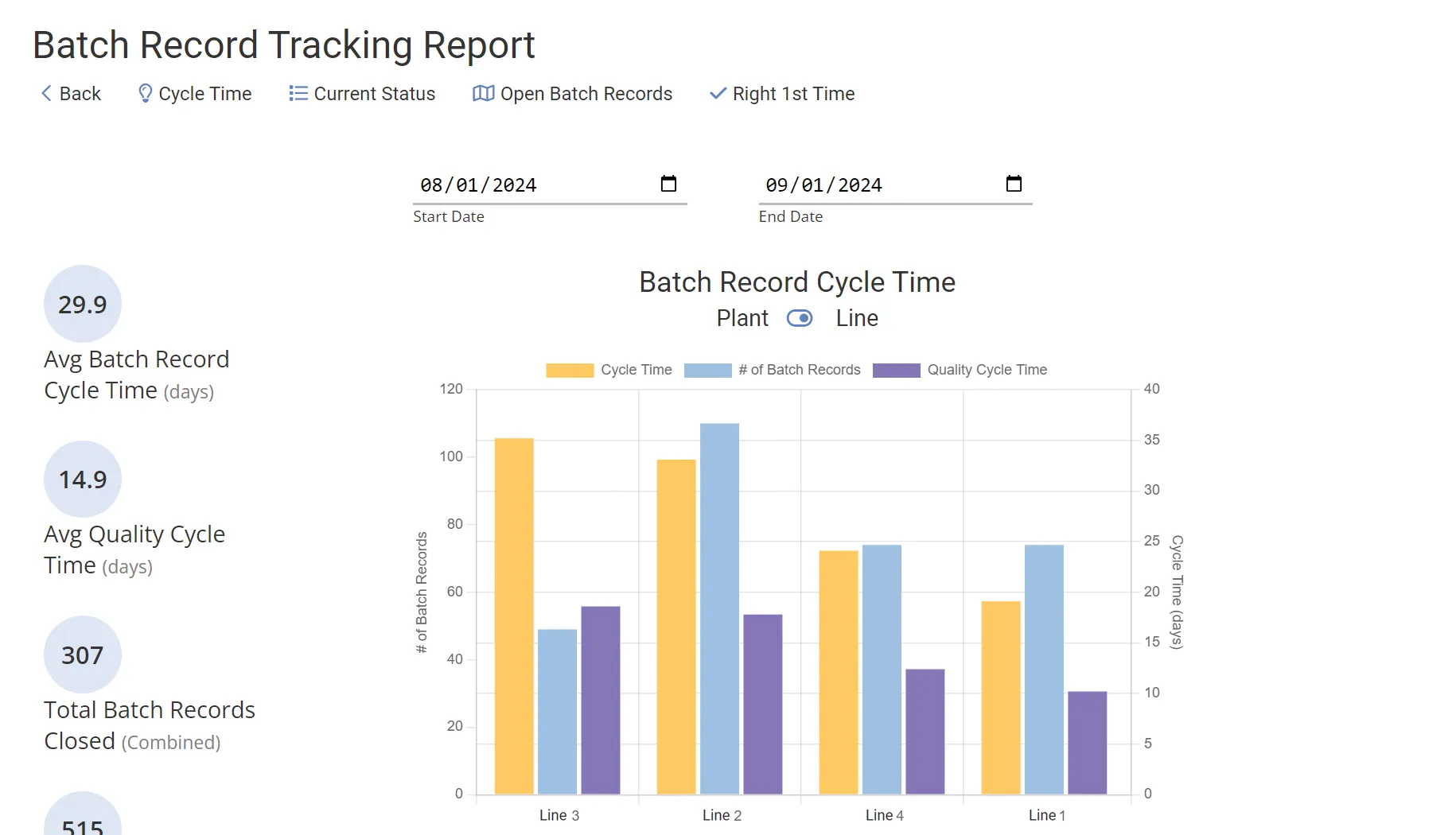
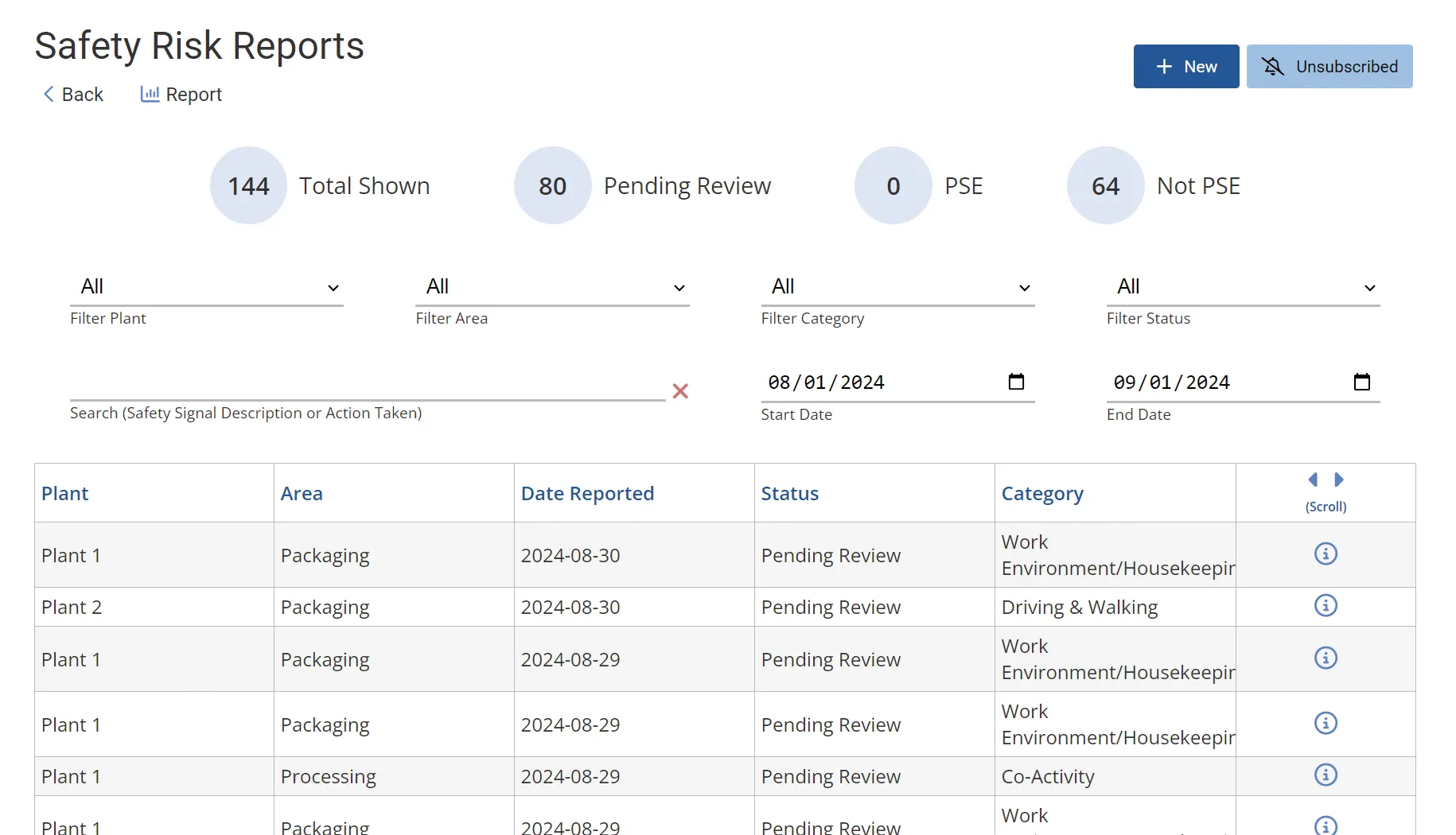
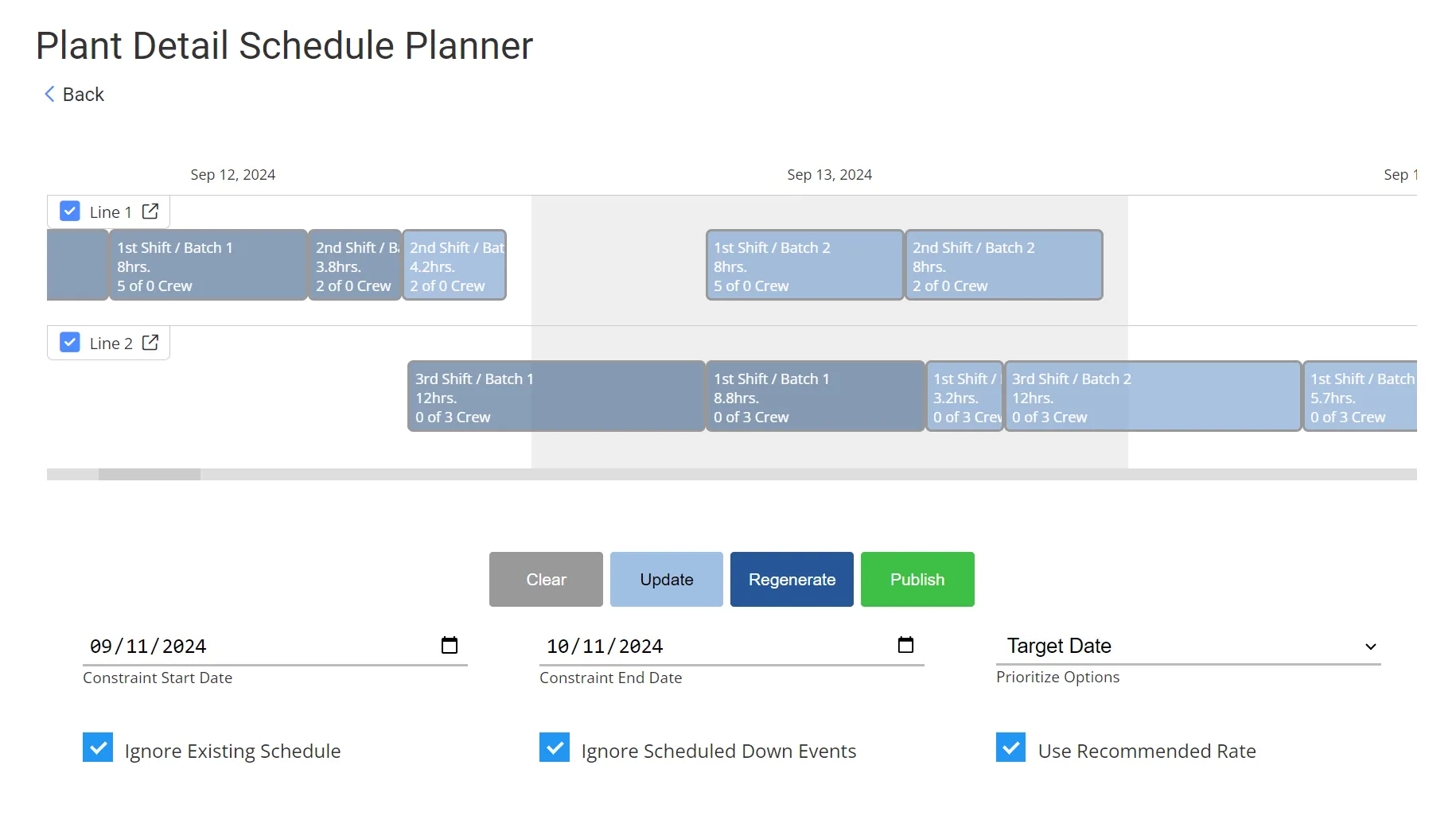
Action Planning
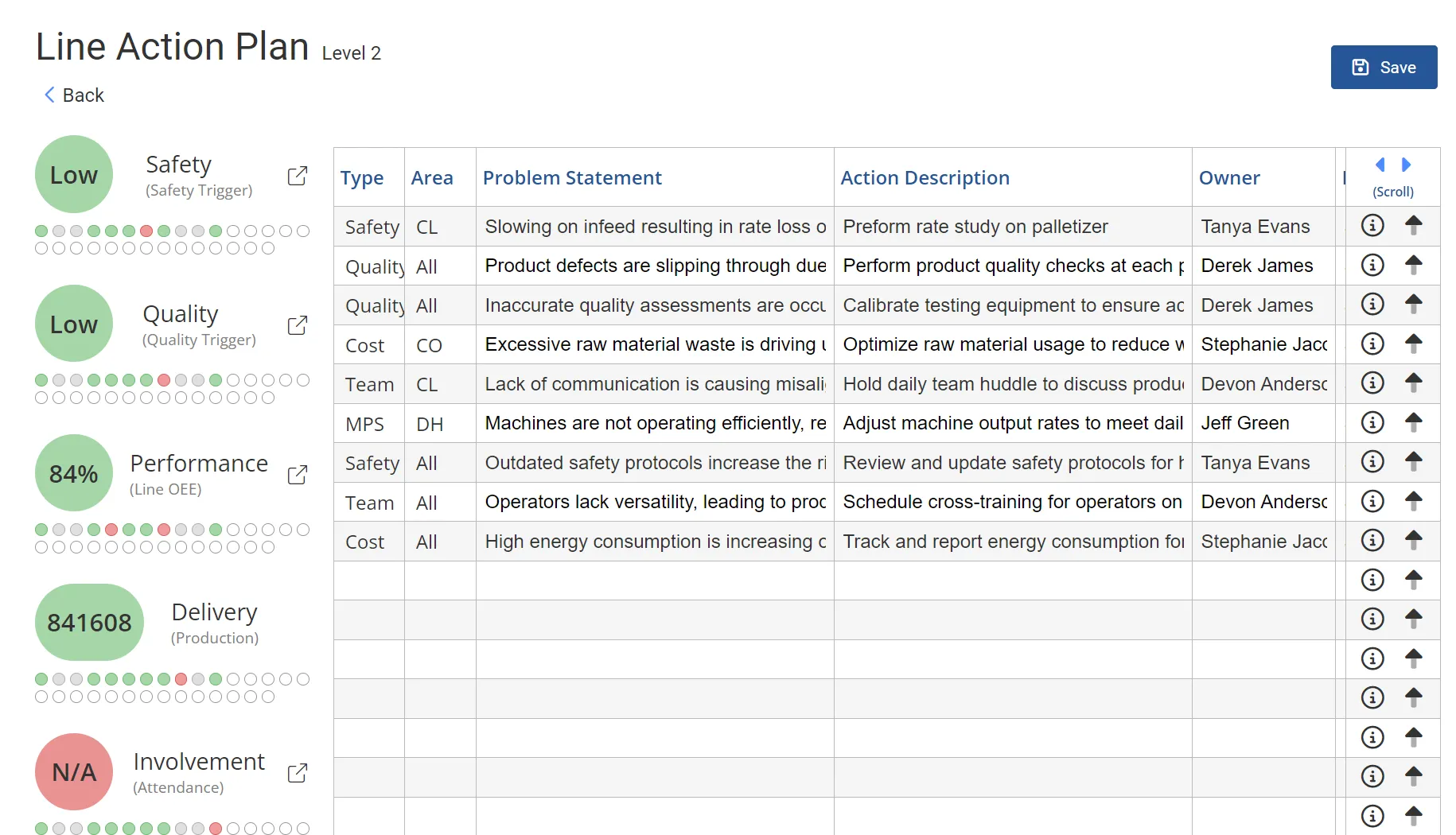
Tracks actions that are generated by the team. It supports a regular task review over a standard cadence or the ability to track long-term action items. Results are also integrated into the DDS process.
Submodules & Additional Features
- Site Action Plan
- Plant Action Plan
- Line Action Plan
- Escalations Between Levels
- Notifications for Upcoming Tasks
Corresponding Modules
Autonomous Maintenance
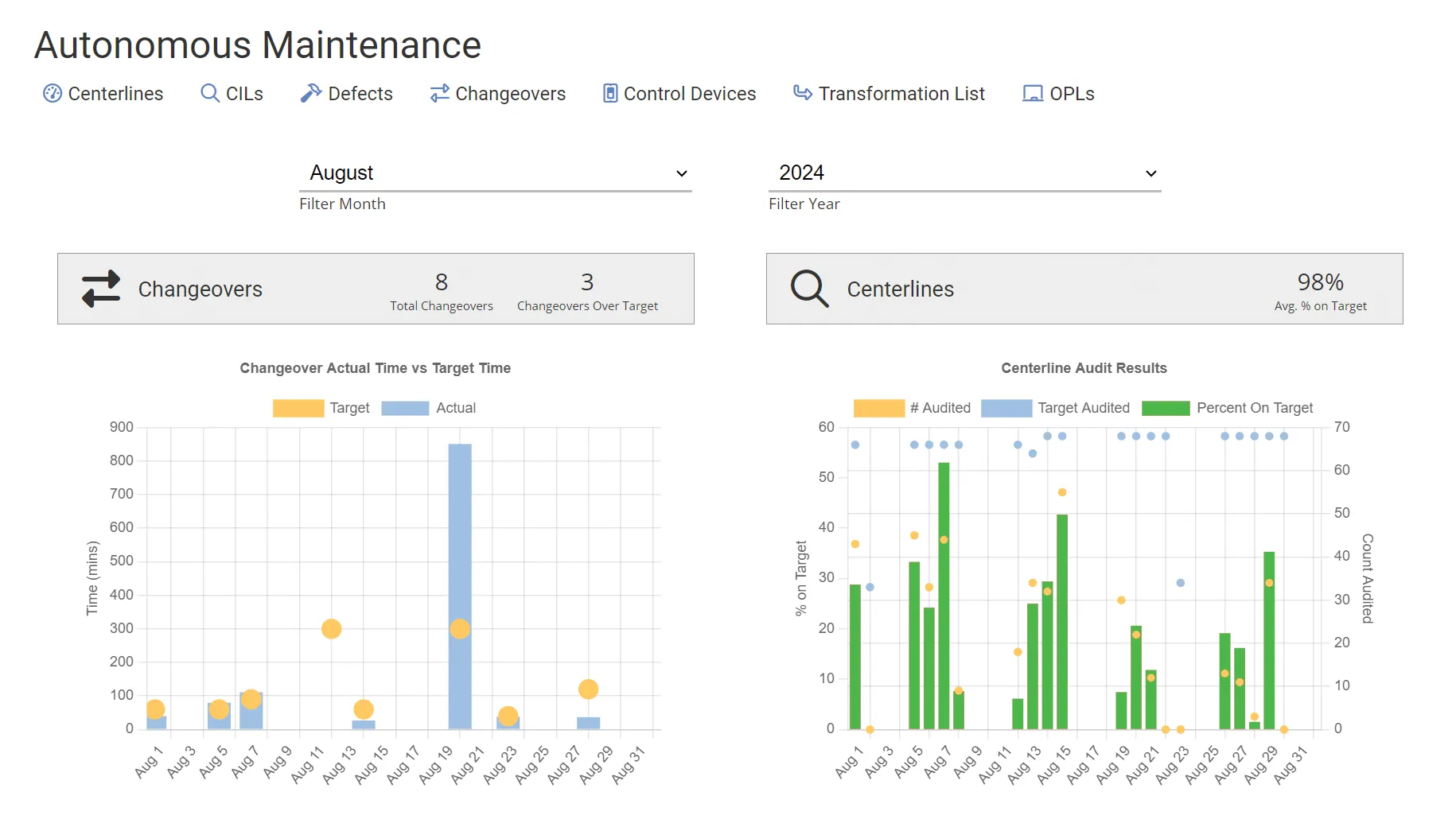
Contains all the AM tools standard to TPM. This gives the team the tools to systematically improve their results and sustain operational excellence once achieved.
Submodules & Additional Features
- Dashboard
- Changeovers
- Centerlines
- One Point Lessons (OPLs)
- Clean, Inspect, Lubricate (CILs)
- Defect Handling
- Control Device List
- Reports by Month
Corresponding Modules
Inventory
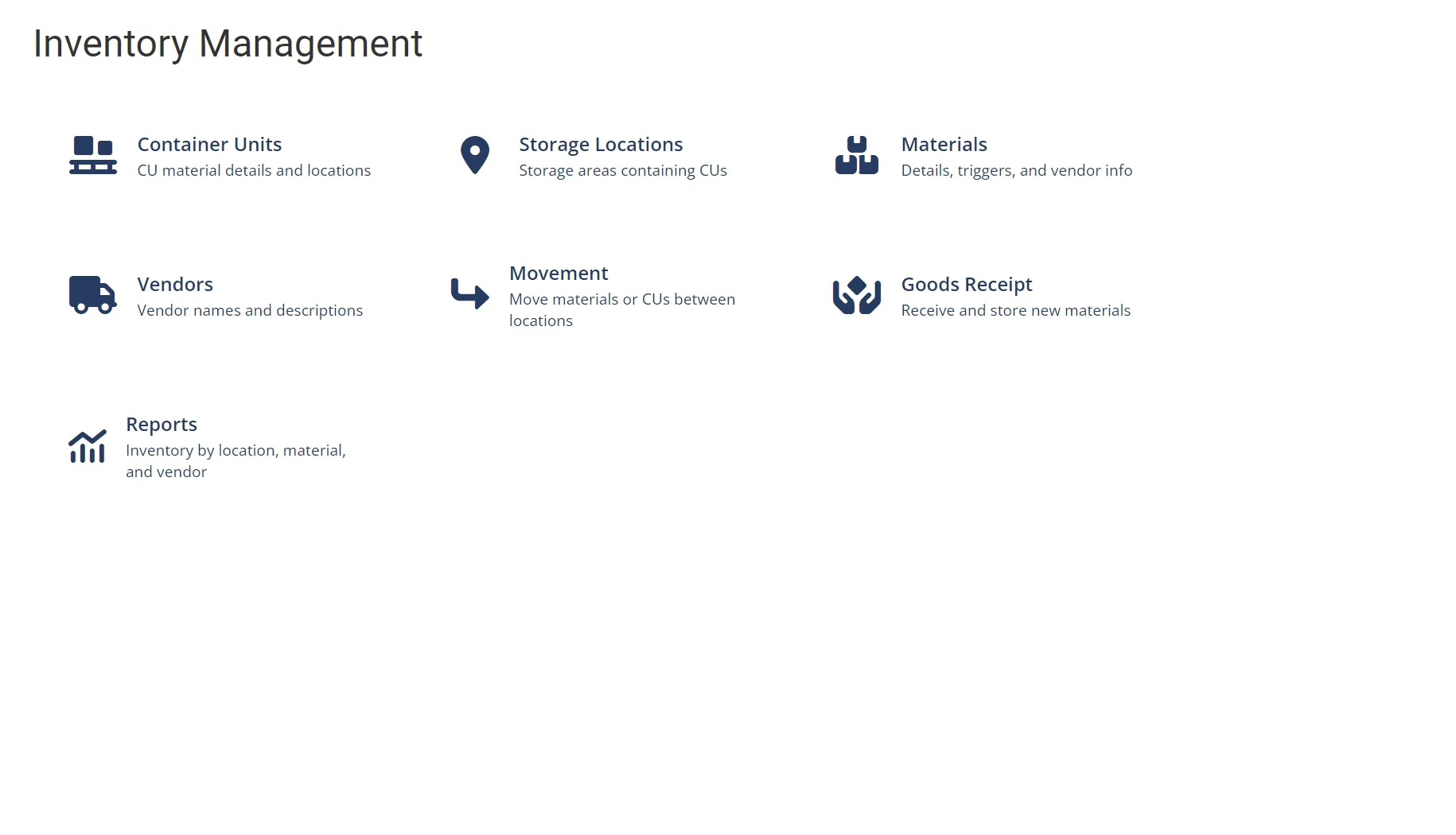
Efficiently import, move, and track inventory throughout your operation. Also manage vendors and storage locations to ensure that your inventory is always organized and easily accessible. With real-time updates, you can maintain accurate records and streamline your supply chain management.
Submodules & Additional Features
- Container Units
- Storage Locations
- Materials
- Vendors
- Movement
- Goods Receipt
- Reports
Corresponding Modules
Loss Elimination
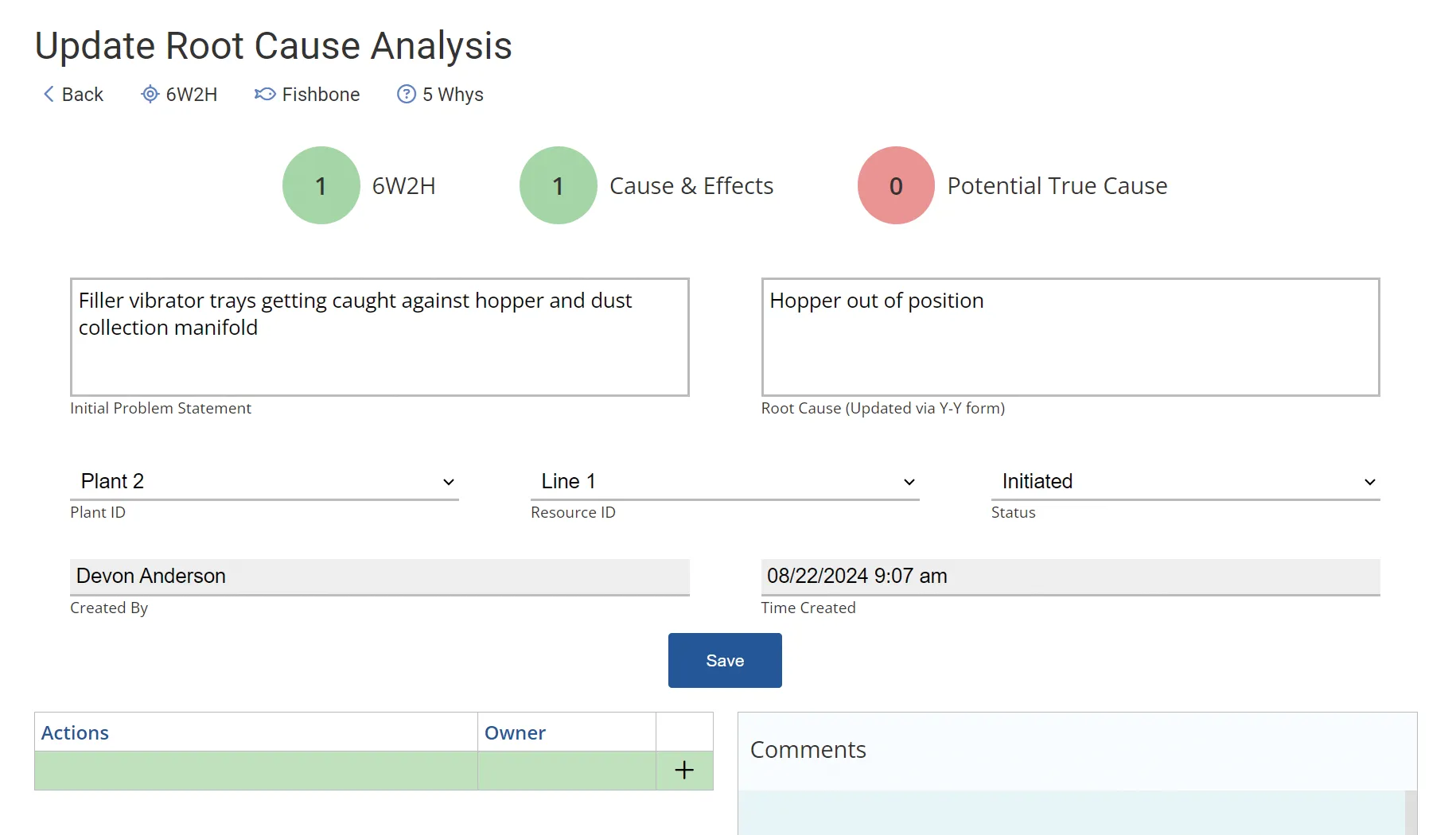
As losses are identified from the Operations module, the LE module gives an individual or a team the tools needed to go from initial problem statement to root cause.
Submodules
- 6W2H/5W2H
- Fish Bone
- Cause & Effect Map
- Why-Why Analysis
- Problem Statement Definition
Corresponding Modules
Operations
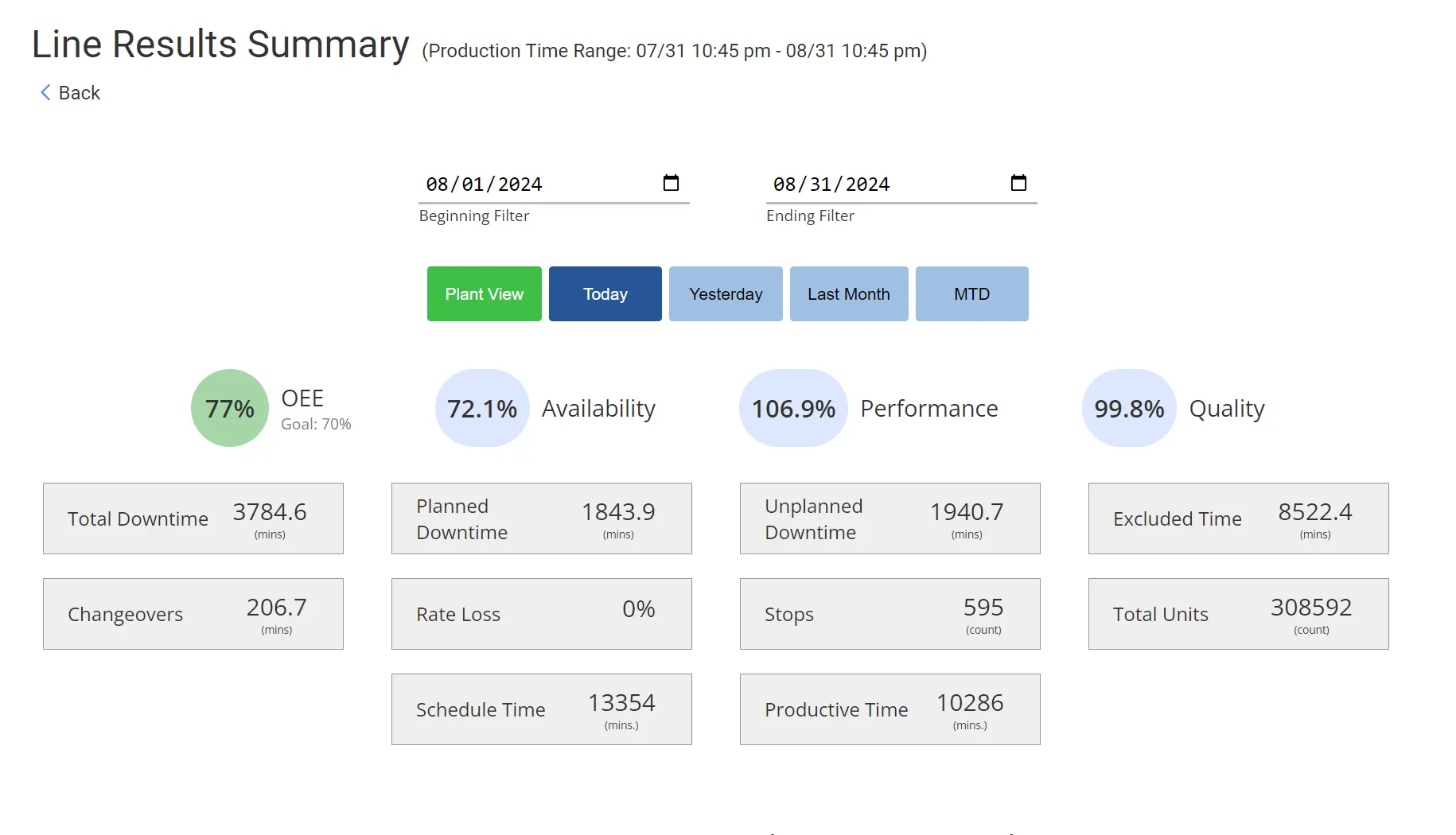
Targets real-time data collection centered on performance. Technicians can get real-time metrics at their fingertips. Then, they can use standardized methodologies to enrich that data before it is analyzed to eliminate losses.
Submodules & Additional Features
- Production Dashboard
- Goals
- Production Data
- Downtime
- Reports
- Real-time Data
- Remote Displays
- Top KPIs
- Multi-level Reports
- Process Confirmation
Corresponding Modules
People
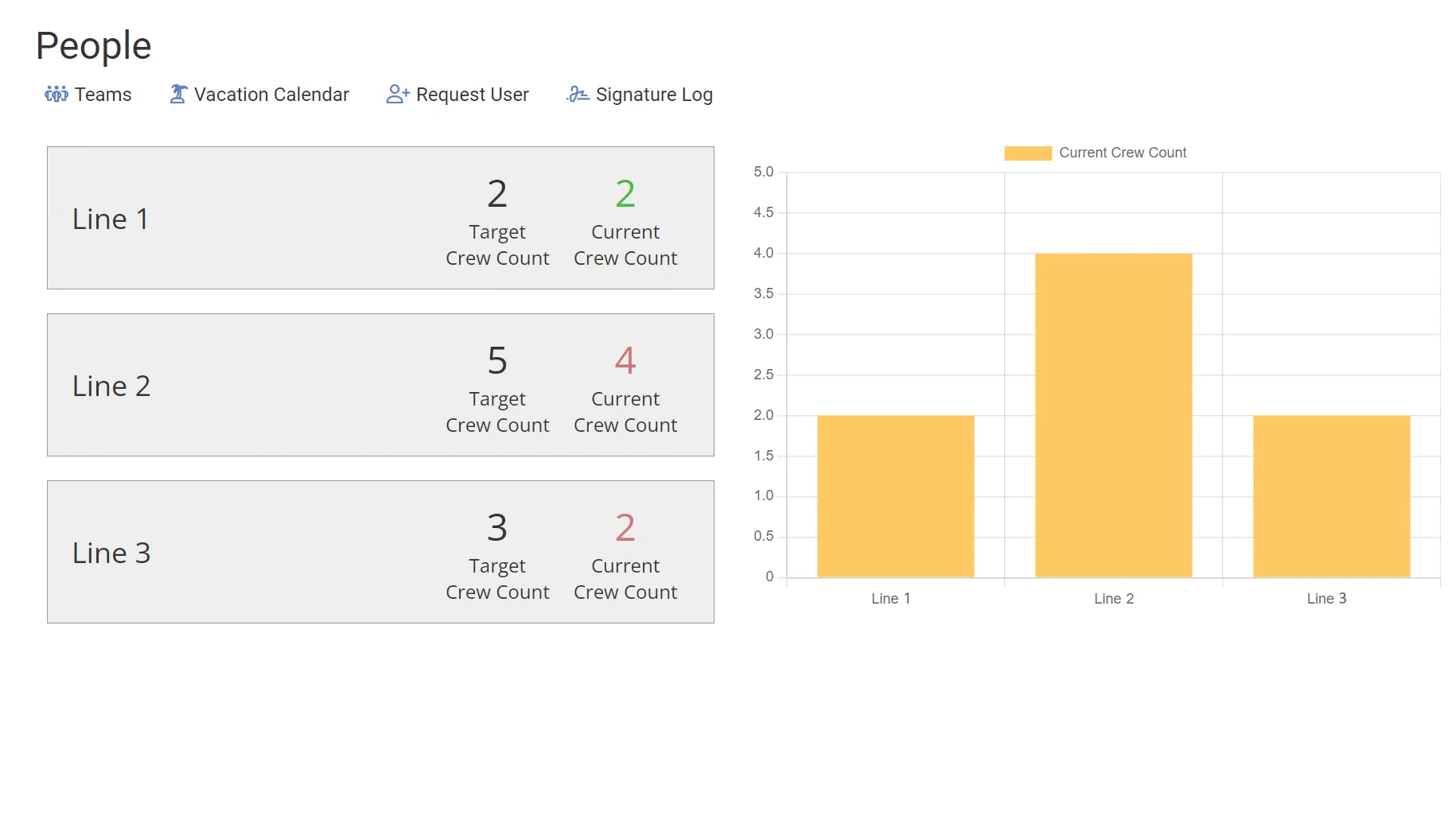
Brings out the best in the technicians and, by extension, the entire site. Some features focus on standard planning / housekeeping items while others target improving the individual and showing them their performance based on the other modules.
Submodules
- Dashboard
- Absentee/Attendance
- Reports
- Vacation Calendar
- User Check-in
- Signature Log
- Teams
Corresponding Modules
Production Execution
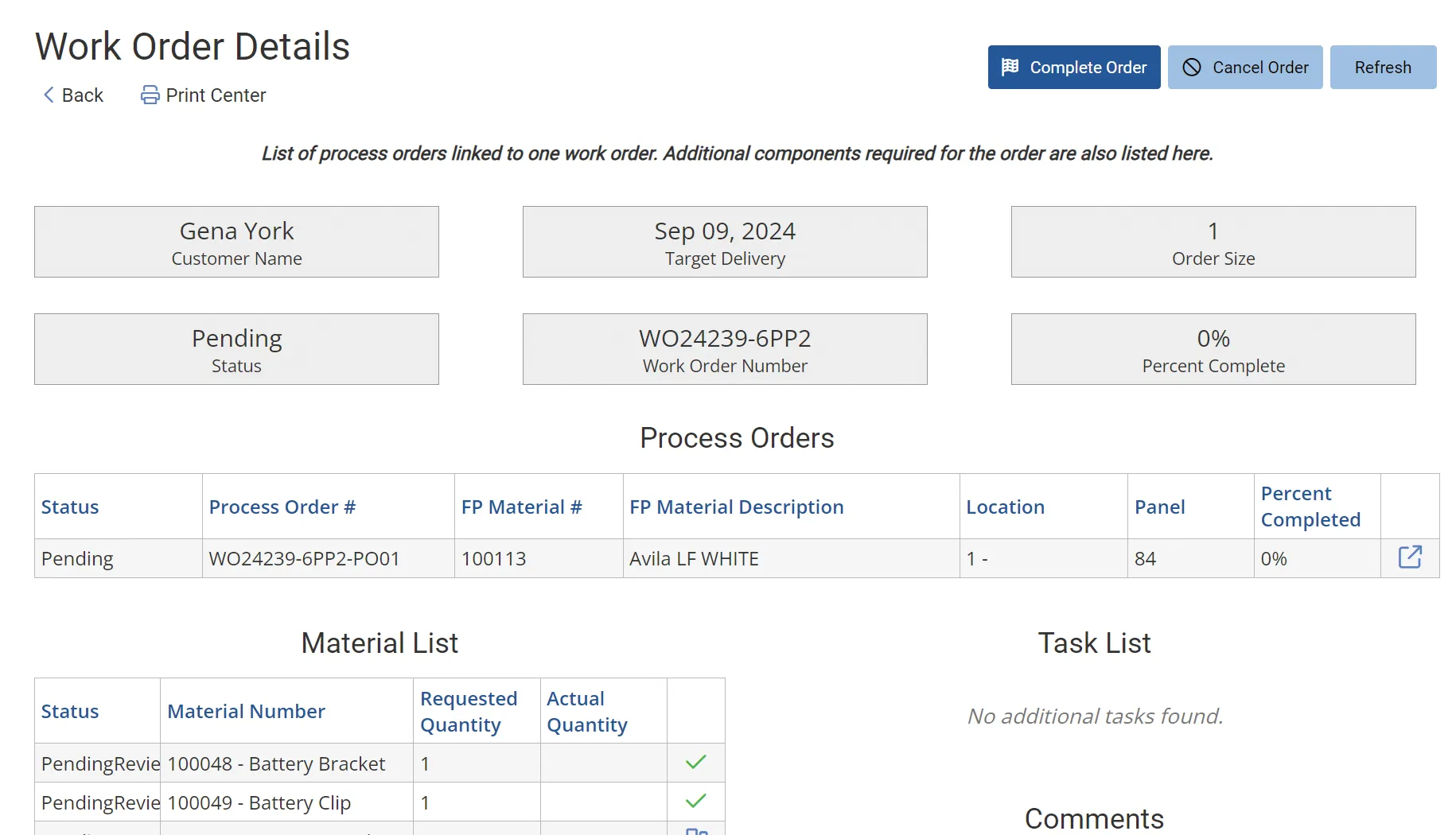
Allows for a highly dynamic, task-based execution model. Here the user can define templates that can be executed by the operations team. These templates can be modeled after batch records, cleaning SOPs, or any other step-by-step documentation that the organization needs to execute.
Submodules & Additional Features
- Production Orders (eBR)
- Cleaning Orders
- Shop Orders
- Approval Workflow
- Highly Configurable
- Several Predefined Actions
- Scheduled Events
Corresponding Modules
Quality
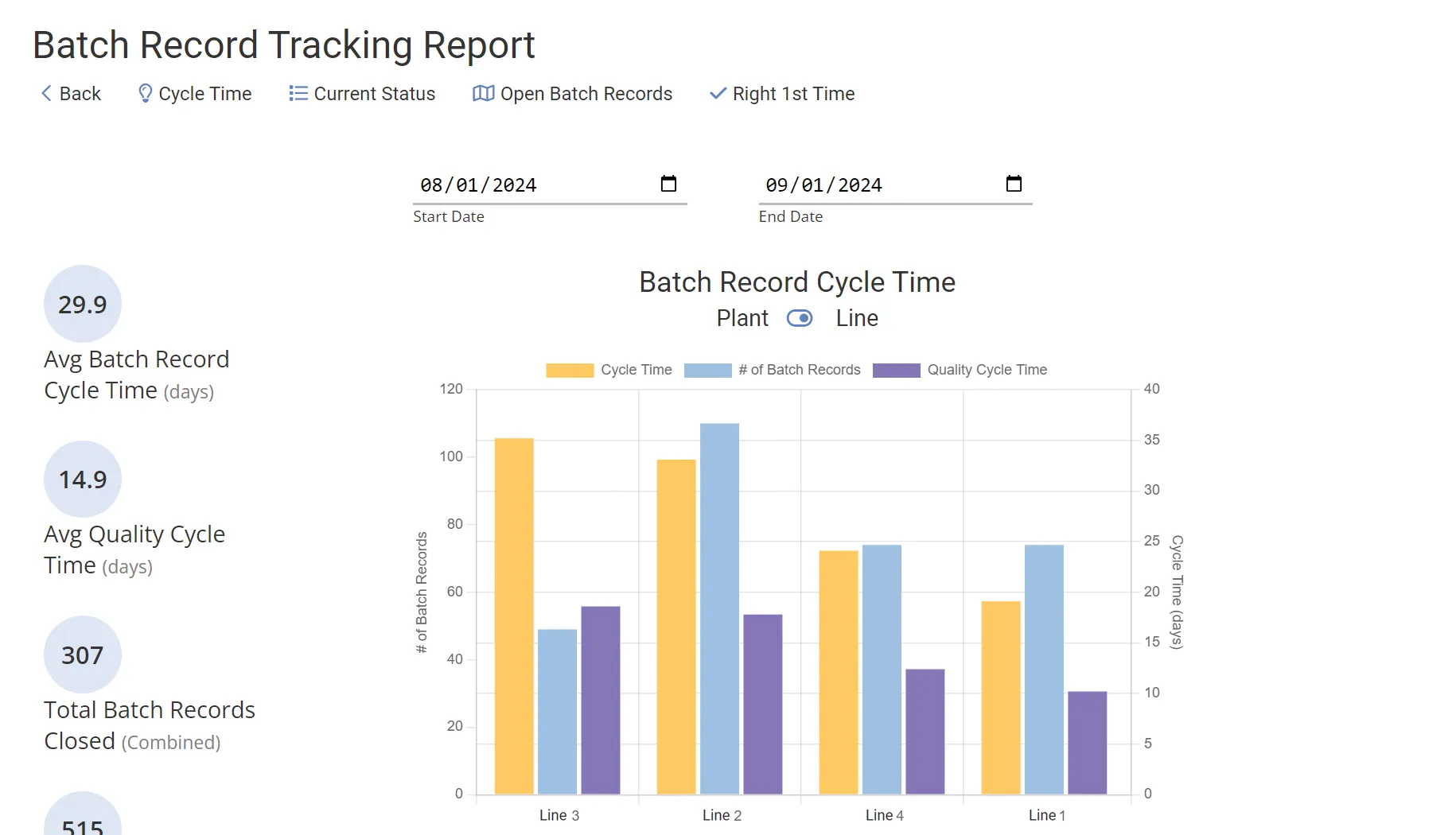
Defines and executes processing/packaging-related quality systems. W&D and lab, however, are not currently in scope. Depending on the requested configuration, this module will be complemented with the PE module for the operational execution of certain quality tasks.
Submodules & Additional Features
- eBR (Configuration)
- BRTD
- BR Review
- Queue-based Workflows
- Confidence Scoring
Corresponding Modules
Safety
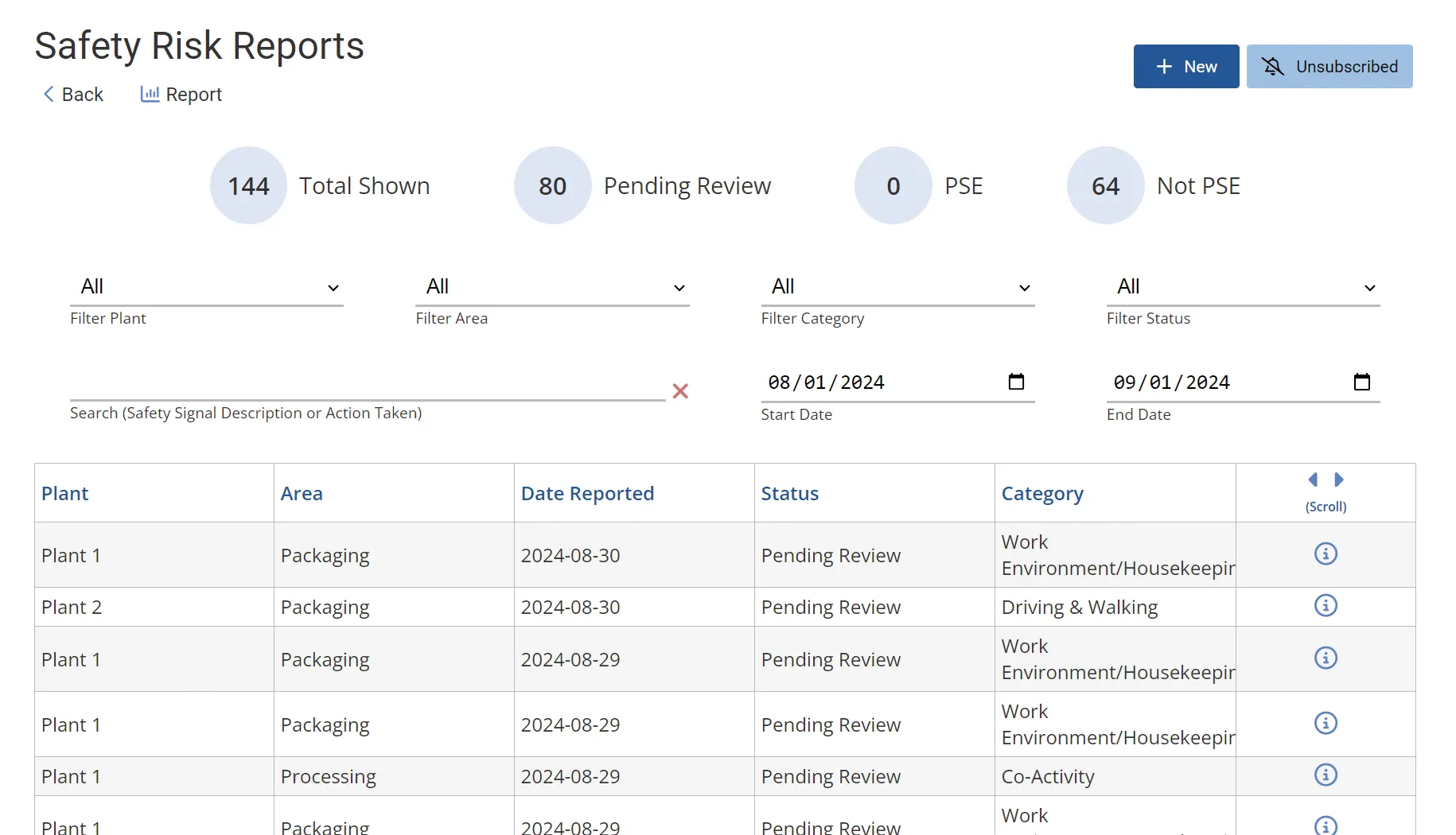
Puts the majority of the site’s safety systems in the hands of the technician. This module prioritizes the flow of safety-related data and ensures that the team can share relevant information and be notified when a safety event occurs. This is coupled with data analytics and reporting.
Submodules & Additional Features
- Weak Signals
- Incident Reports
- MSV / BOS
- Housekeeping Tour
- Work Permits
- Inspections
- OPL Integration
Corresponding Modules
Supply Stream
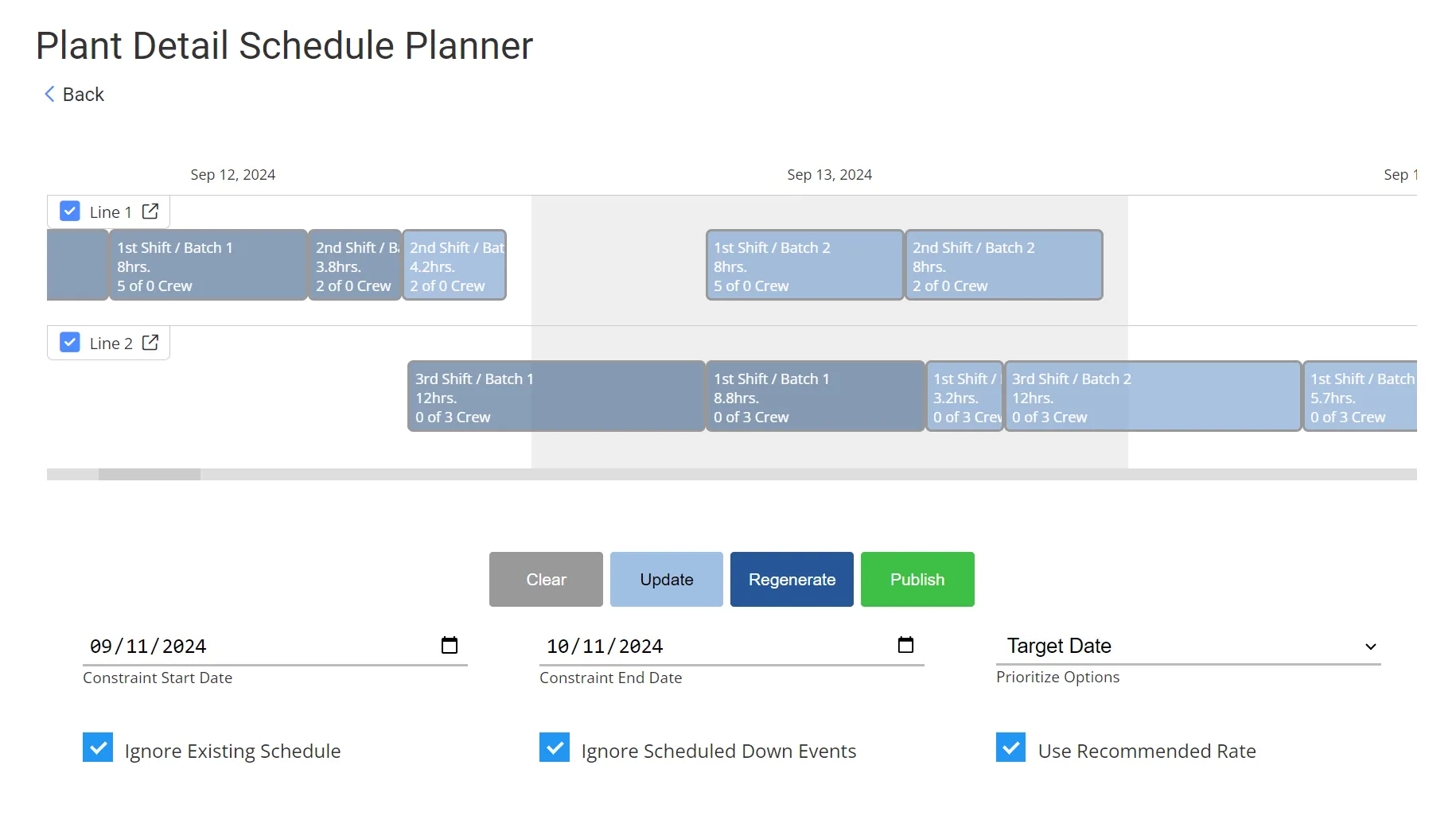
Gives teams the ability to see the production demand needed to run the business. Here they will have access to their production schedule and products defined inside the system. Also allows for detailed scheduling (2-5 week horizon), taking into account several variables to improve accuracy.
Submodules & Additional Features
- Scheduling (Production)
- Products
- Shift Events
- Shifts
- Downtime Schedule
- Detailed Scheduling
- Production Lead/Lag Times